Sustainability
At OrthoLite, we made the choice from the very beginning to be good to the planet.
SUSTAINABLE COMFORT AND PERFORMANCE
OrthoLite has a stalwart commitment to work with the global footwear industry to become less impactful. From investing in responsible manufacturing practices in our seven owned facilities, to innovating our product with more sustainable materials solutions, to striving to improve the footwear manufacturing supply chain, our focus remains on lessening our impact and supporting the health of our planet.
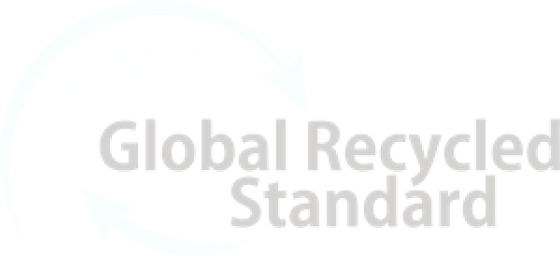
GRS CERTIFICATION
The Global Recycled Standard (GRS) is intended for use with any product that contains at least 20% Recycled Material. Each stage of production is required to be certified, beginning at the recycling stage and ending at the last seller in the final business-to-business transaction. READ MORE
sustainable production
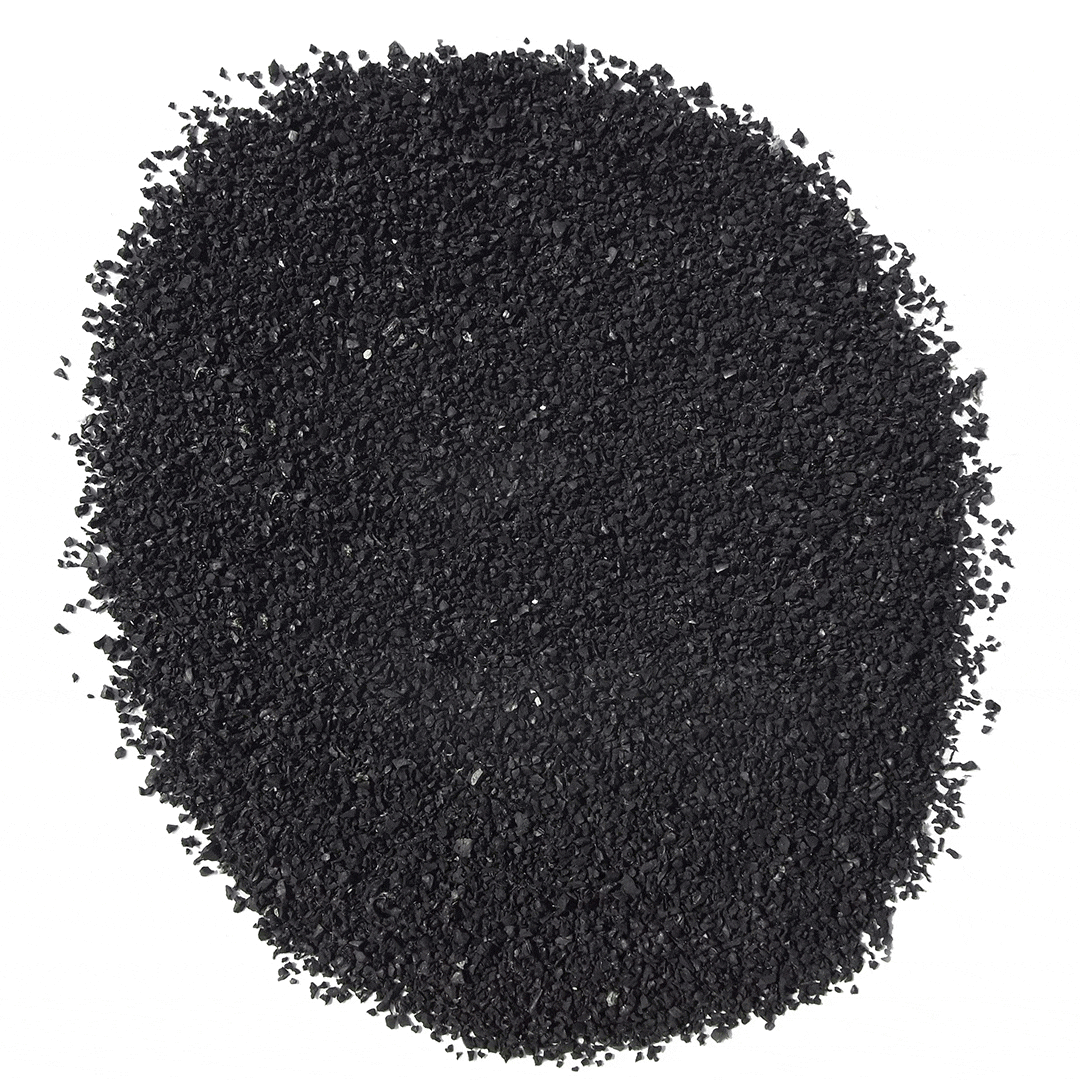
RECYCLED RUBBER
Take a good look at any OrthoLite insole and you’ll notice the tiny black flecks. That’s part of our proprietary technology—recycled rubber from the production of outsoles—and we’ve used it in every insole we’ve ever made. It adds resiliency, breathability, cushioning and comfort—and prevents over 1.32 million pounds of recycled rubber from entering landfills each year. It helps us do our part within the footwear community to close the loop within the production process.
BIO-OIL TECHNOLOGY
Our proprietary plant-based bio-oil comes from castor beans—a non-food source that doesn’t compete with food crops and uses very little water to grow. The rapidly renewable plant has been naturalized in warm climates all over the world, and can grow ten feet in a single season. The use of castor oil reduces the need for petroleum in our products and uses fewer natural resources to produce. It allows us to provide our customers with less-impactful insole solutions that still offer long-lasting comfort and performance.
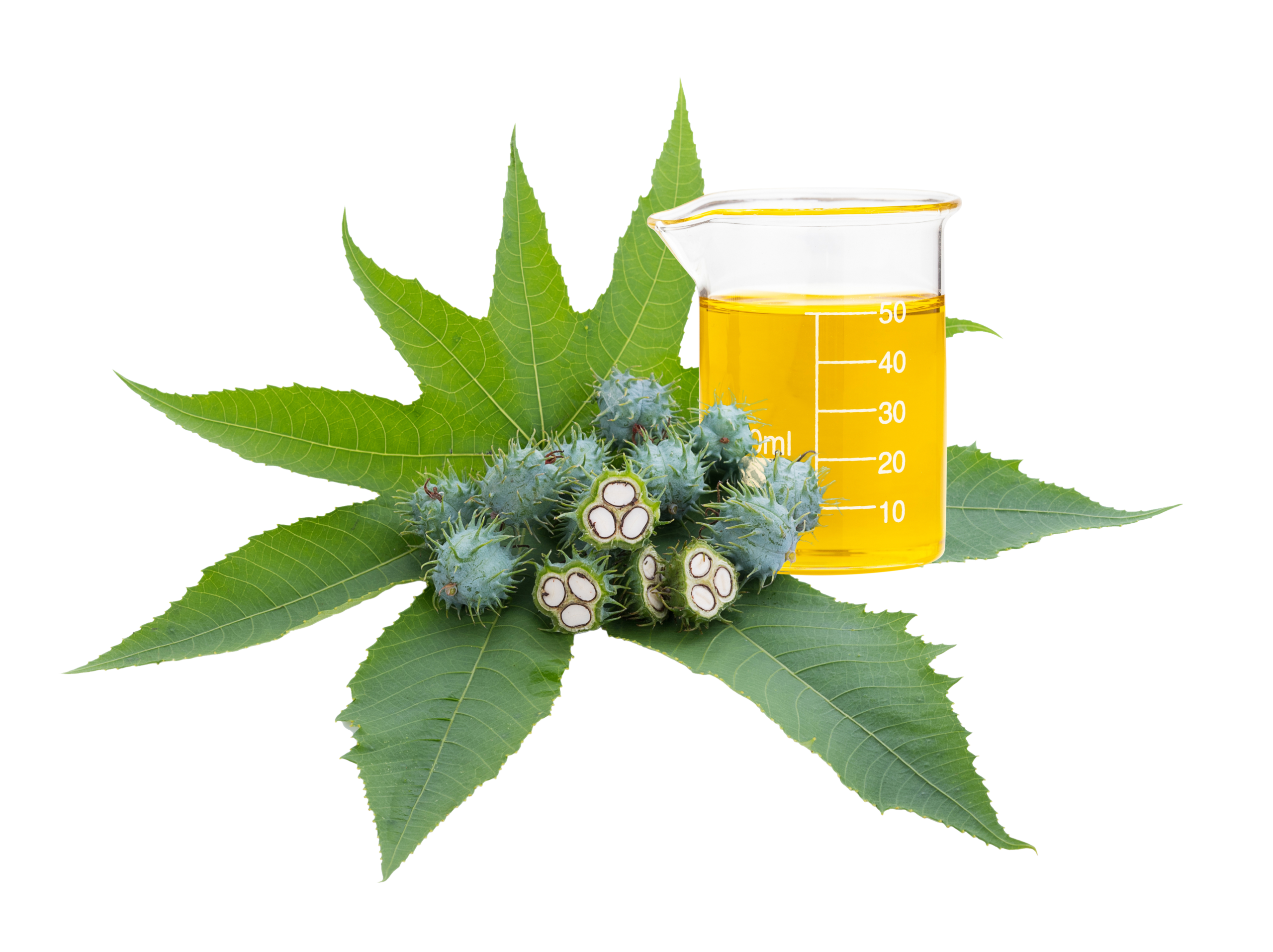
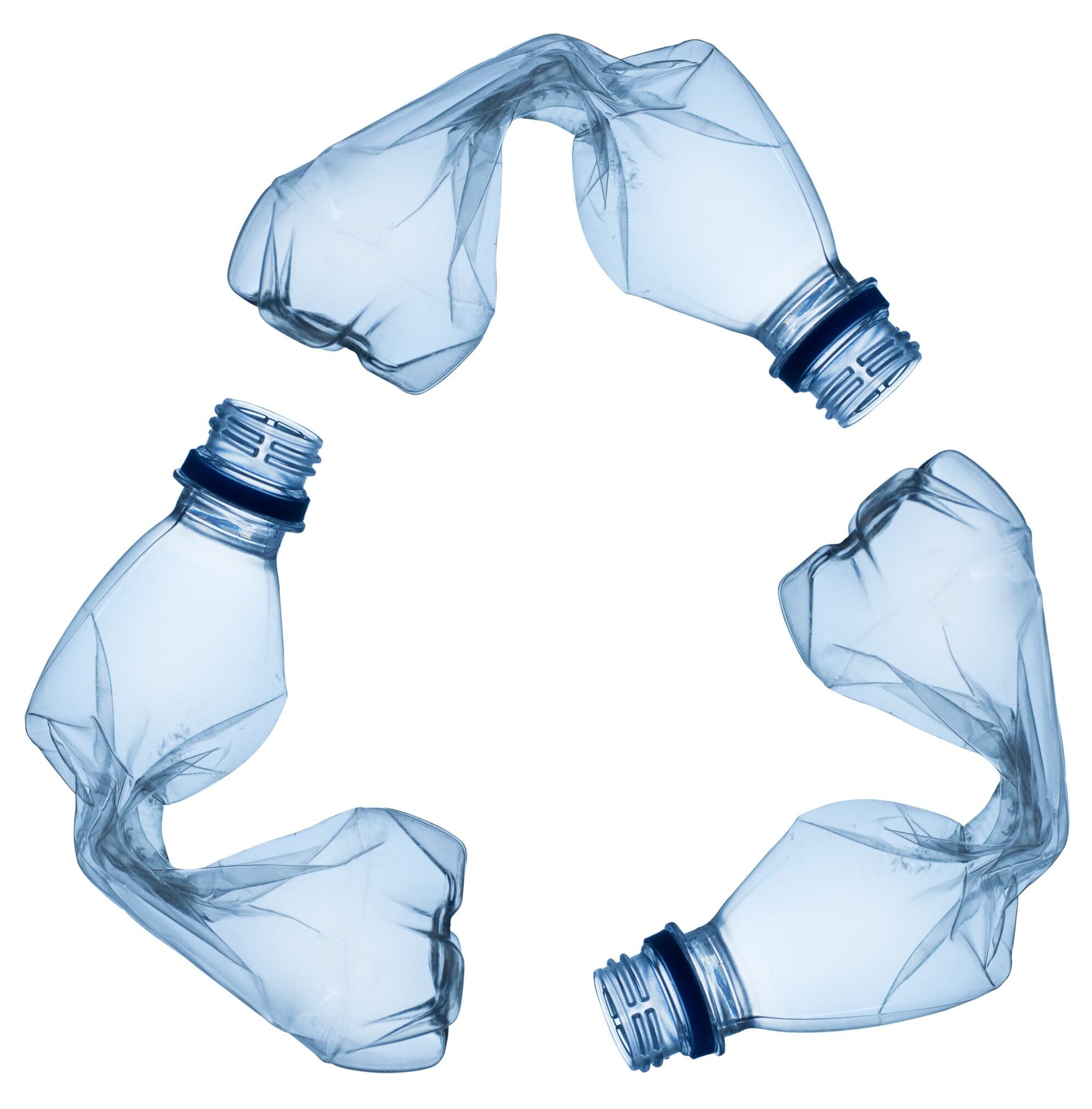
ZERO WASTE INITIATIVES
We have invested in the continued development of more sustainable solutions that optimize our supply chain from end to end by capturing and repurposing all waste material. The result is a range of product solutions with 5% to 98% recycled content.
LOCAL FOR LOCAL
Operating 10 locations across 6 countries and 3 continents and proximity to T1 factories provides an invaluable benefit for our brand partners. This local-for-local approach provides a more efficient means of transporting finished goods and reducing the amount of time and energy used to transport them.
Our Vietnam Solar Installation
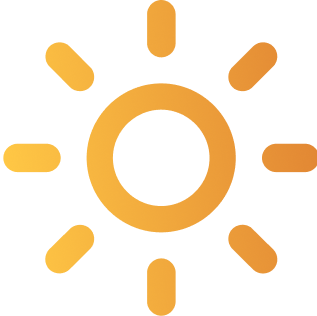
4,320
solar panels
INSTALLED
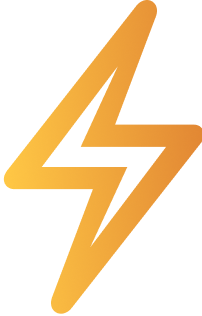
2
megawatt output
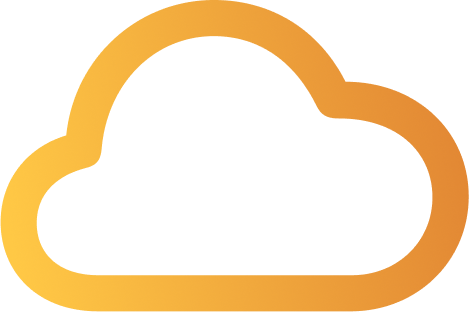
3,500,000
kg of carbon offset
Air Purification
The advanced air filtering and treatment equipment at our factories filter out airborne particles and circulate purified air, keeping our employees healthy and protecting the environment.
Water Recycling
We process and reuse wastewater from our manufacturing facilities around the world. When the recycled water can’t be reused, our system converts it into solid refuse that’s treated to the strictest environmental standards.
Solar Energy
Our factories use clean solar energy to heat water for manufacturing and to warm our facilities—reducing our dependence on fossil fuels. On cloudy days, our factory uses heat powered by an efficient air compressor, limiting our environmental impact.
SUSTAINABLE PACKAGING
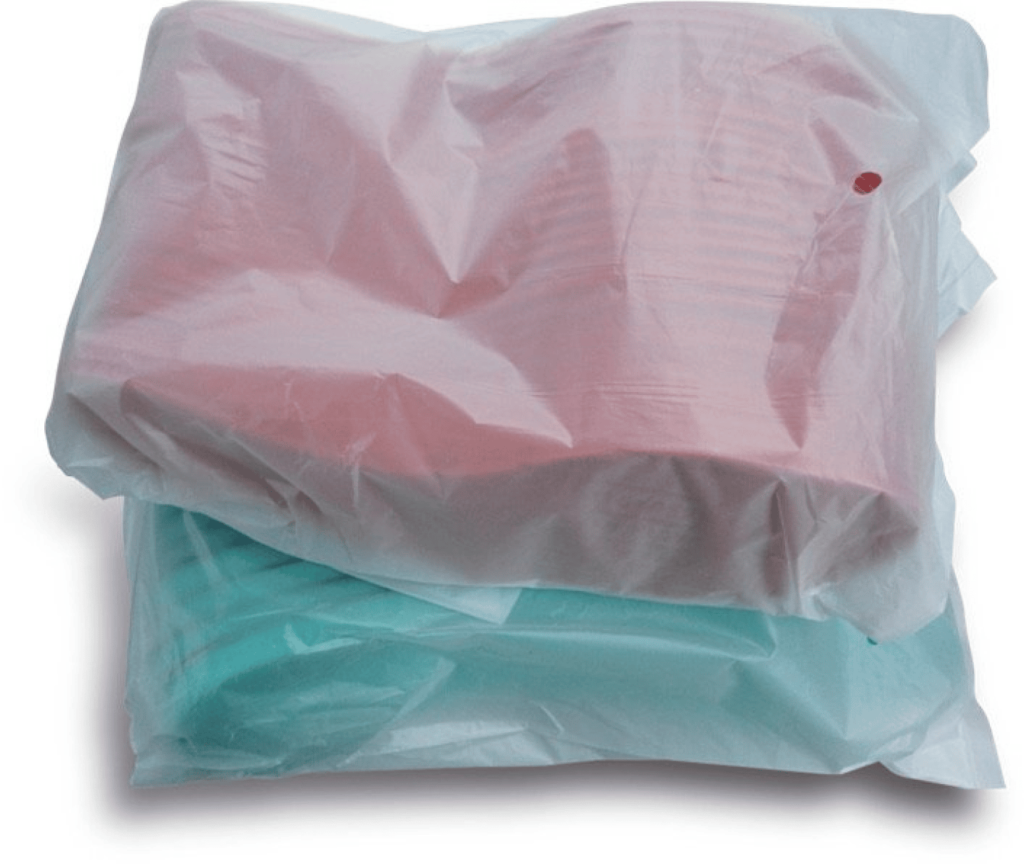
ECO BAGS
Ordinary polybags take hundreds of years to decompose, causing pollution and trapping marine life. That’s why we pack and deliver our products in bags made with calcium carbonate sourced from natural limestone. The bags are waterproof, tear resistant, pest resistant— and biodegrade naturally in 10-12 months.
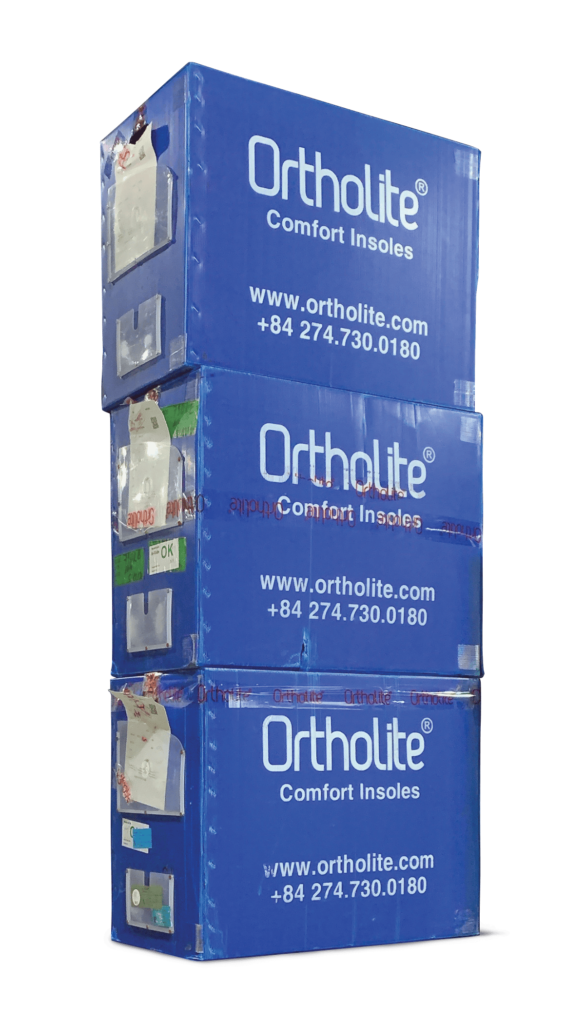
BLUE BOX PROGRAM
As an alternative to shipping products in cardboard boxes, we can support our brand partners’ sustainability goals by transporting our products to footwear factories in 100% recyclable, reusable blue boxes. By reducing the use of cardboard, we save thousands of trees, decrease our carbon footprint, and eliminate the need for hundreds of thousands of gallons of water a year.
sustainable products
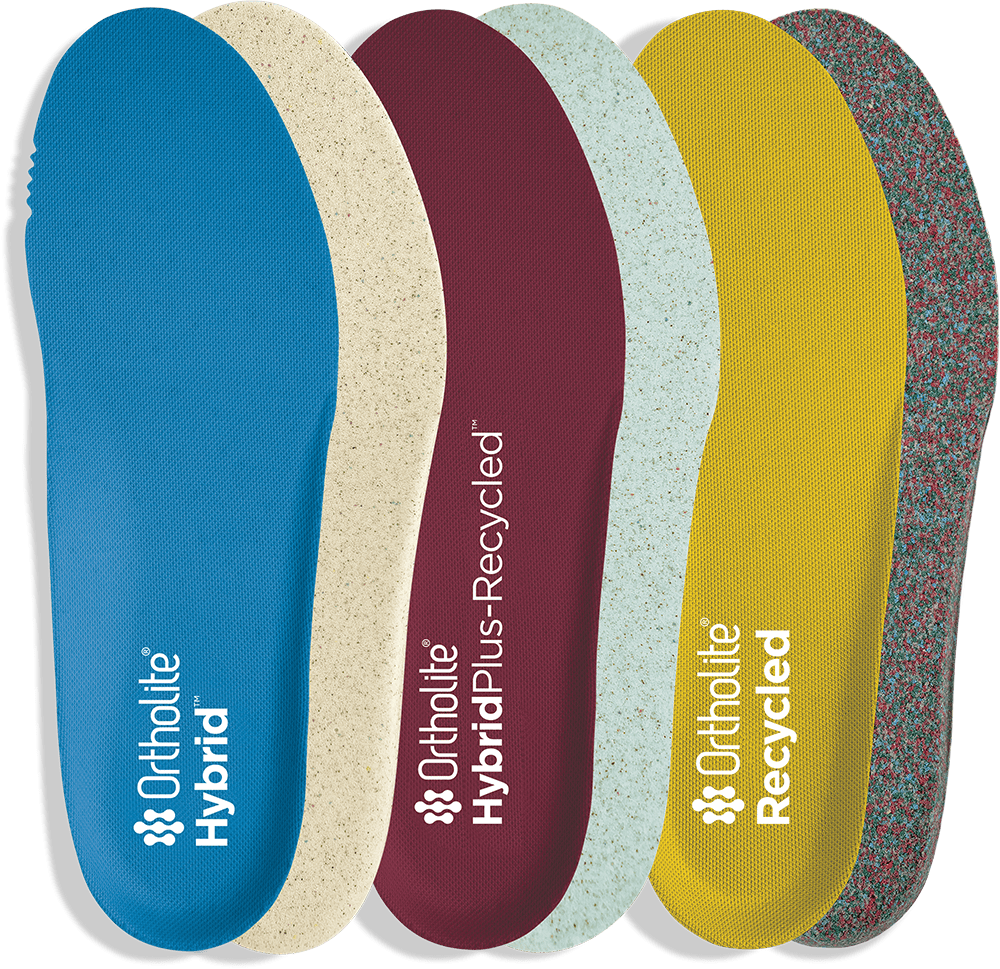
Hybrid Technology
OrthoLite® Hybrid™ gives our partners the unprecedented ability to up the eco-content in their insoles.
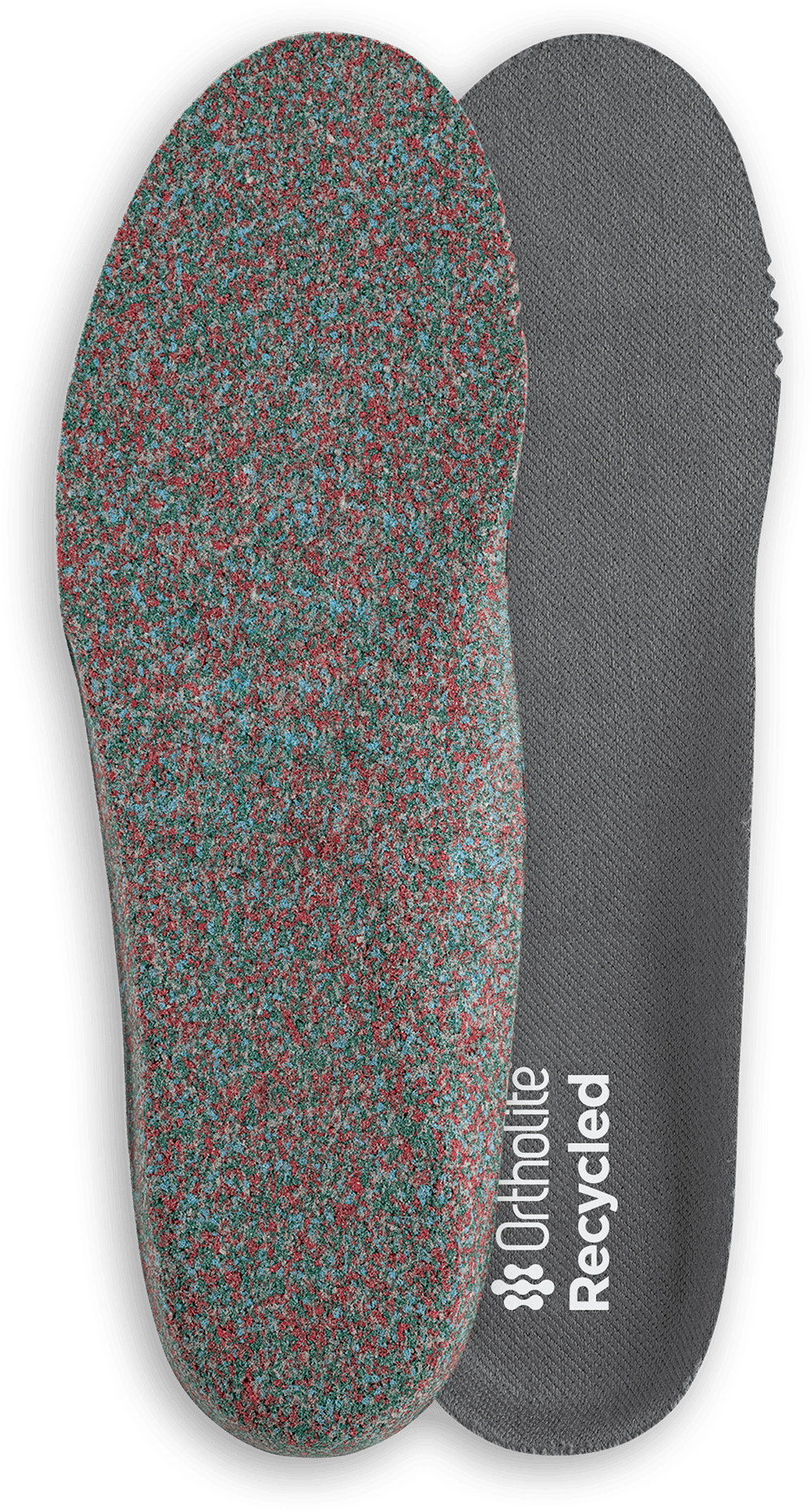
OrthoLite® Recycled™
Consisting of 98% post-production waste material, OrthoLite® Recycled™ gets us closer to the end goal of ZERO waste.